

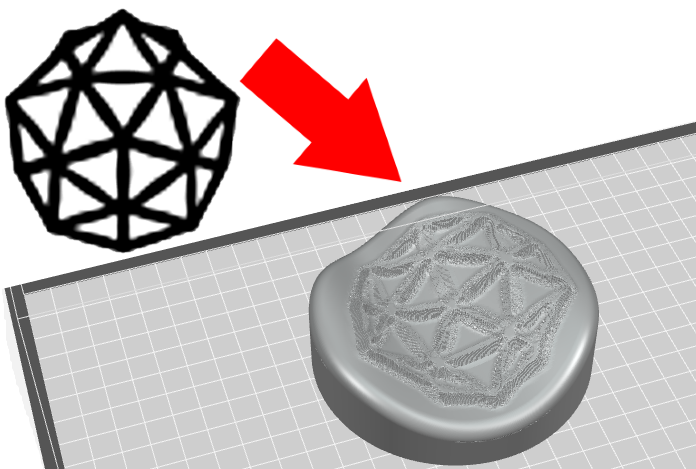
- #SOLIDWORKS 2017 WORKING WITH AN STL FILE PRO#
- #SOLIDWORKS 2017 WORKING WITH AN STL FILE SOFTWARE#
- #SOLIDWORKS 2017 WORKING WITH AN STL FILE PROFESSIONAL#
To change the file’s quality when saving in STL format, simply press ‘options’.

In many CAD software, an STL file’s quality can be controlled when it is being created. The same is true for the print quality of curved surfaces. Import / export DXF and DWG files compatible with most other CAD solutions like AutoCAD. Let’s take a cylinder ready to print with a diameter of 100 mm.ĭepending on the quality of your STL file, issued from your CAD, the diameter could exhibit a difference of 325µm versus virtually 0µm with a high quality STL. Here are a few examples of the dimensional accuracy and quality surface finish attained with the source file only, regardless of the equipment’s adjustments or printing quality. The expert team at Fathom has identified the most common pitfalls and guarantees that this STL Guideline document will save you time and ensure that your 3D printed parts accurately represent your idea.When the time comes to produce printed parts with tighter tolerances, or if you want to get the smoothest surface finish possible out of your printer or your service supplier, the importance of your STL files’ quality cannot be overstated. After exporting the file, reimport it by selecting to File>Open in SOLIDWORKS and browsing to the file. Since SOLIDWORKS is built on the Parasolid modeling kernel this reduces the chances of anything coming back broken to almost zero. Our engineers are able to address the most common mistakes and potential errors with STL file preparation, as even the most popular CAD packages can pose difficulties during STL file export. When exporting a file in this way, I’d highly recommend saving the file as a Parasolid file type. Working with Fathom provides immediate and comprehensive access to the most relevant equipment and experience in advanced manufacturing, engineering, and prototyping. We recommend combining the bodies into a single solid before exporting into an STL. Those, who regularly work with STL files, clearly understand the.
#SOLIDWORKS 2017 WORKING WITH AN STL FILE SOFTWARE#
Intersecting faces usually lead to failures since the software doesn’t recognize which areas are inside or outside of the model. Unlike a CAD file, an STL file is an approximation of the original design, and contains.
#SOLIDWORKS 2017 WORKING WITH AN STL FILE PRO#
Or you are getting Autodesk Inventor Pro v2017 64bit has stopped working. details of over 40 SOLIDWORKS World 2017 Product Showcase Preview: Robotics.
#SOLIDWORKS 2017 WORKING WITH AN STL FILE PROFESSIONAL#
Overlapping & Intersecting Triangles / / Overlapping and intersecting triangles may produce areas too small to print. Autodesk Inventor Professional the ultimate 3D CAD software for 3D mechanical. Rajput Strength of materials Download Go Kart 3D CAD Model for AutoCAD. Solving any issues with your models in the native CAD software tends to have better results. We recommend removing noise shells for cleaner contours. Unwanted meshes and noise shells are typically created in error during an STL export. Multiple Shells / / Typically, it’s ideal for your STL to be made of one shell body for printing. It may be necessary to edit or re-export of the original 3D CAD file.
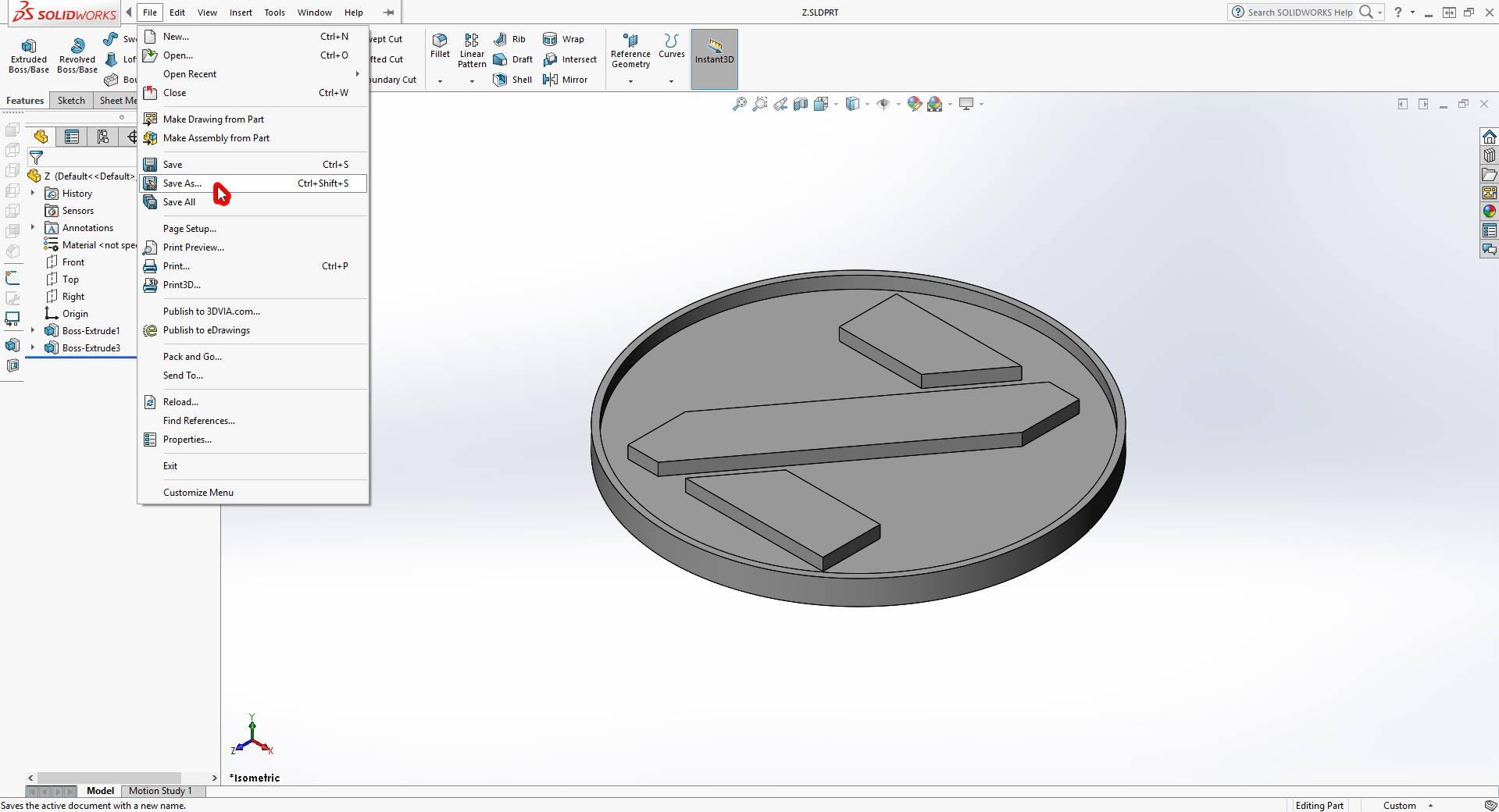
This is sometimes an easy fix within the STL, but that is not always the case. Holes / / Missing triangles from a region prevents a closed mesh. Adding thickness or clearance where needed can sometimes help solve faulty edges. This requires STL repair and we recommend re-modeling the areas where the boundary edges were detected in the native CAD software. Many times, bad edges that are very close to one another may be stitched together to close the mesh. Simple STL editing software will enable you to flip the direction of the normal to correct the issues.īad Edges / / The edge of a triangle is not adjacent to another triangle edge. Because of this, slicing software will be unable to create contours for printing. Inverted Normal / / A triangle’s normal is flipped the wrong way which creates an open mesh.
